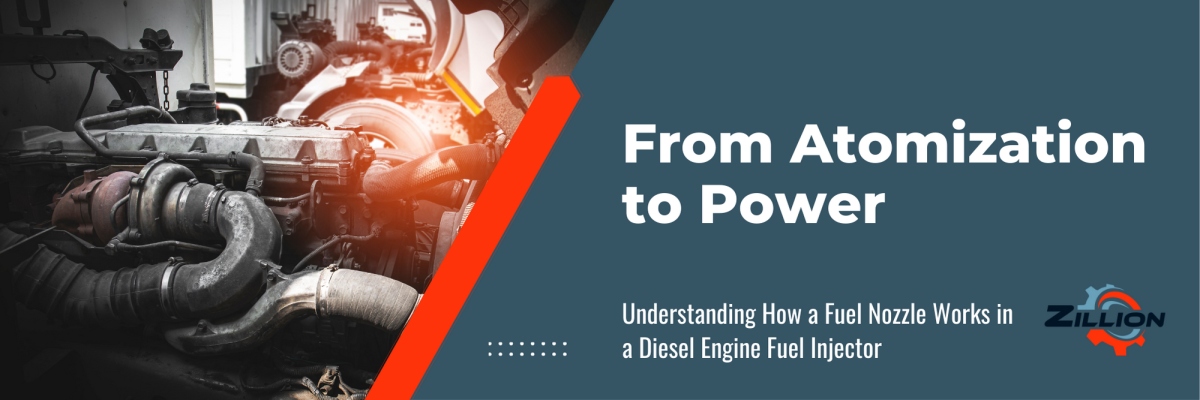
Diesel engines have enabled humans to build our modern world. In the trucking industry, diesel engines have powered semi-trucks for decades. Over the decades these engines have become more powerful while also becoming increasingly efficient and cleaner. To achieve this the engines have also become more complex.
--- Read More Tag ---
The fuel nozzle in a diesel engine fuel injector plays a crucial role in the combustion process. If you repair diesel engines it is important to understand how each part of the fuel system works so that you can diagnose issues correctly when they occur.
This is how it works:
- Fuel Delivery
- Injector Nozzle Opening
- Fuel Atomization
- Combustion
Fuel Delivery
Diesel fuel stored in the fuel tank is pumped into the fuel system by a fuel pump and delivered into the combustion chamber by the fuel injector.
Injector Nozzle Opening
As the piston nears the top of its path, an electrical signal is sent to the solenoid attached to the injector nozzle. This causes the injector needle to lift, allowing high-pressure fuel (up to 37,000 psi) to flow through the nozzle.
Various Types of Fuel Nozzles
- Fan-spray design: Generates a fan-shaped spray pattern of fuel droplets. This type is often used in gasoline engines to improve fuel distribution and combustion efficiency.
- Multi-hole design: Commonly used in high-power engines. They are placed in the combustion chamber and vary in design for optimal fuel dispersion, enhancing performance, efficiency, and emissions control.
- Pintle design: Features an inverted conical tip generating a conical spray pattern. They are strategically positioned to optimize the fuel-air mixture and stand out for its historical significance in fuel injection engineering evolution.
- Single-hole design: Operates with a single, small aperture to deliver fuel, producing a fine mist of droplets. Typically used in low to medium power engines.
- Cone-spray design: Designed to produce a cone-shaped spray pattern of fuel droplets, enhancing fuel and air mixing in diesel engines for improved combustion efficiency.
- Split-injector design: Equipped with multiple orifices dedicated to specific engine cycles. They are commonly used in multi-cylinder engines for precise control of fuel delivery to each cylinder.
Fuel Atomization
The fuel is expelled through a tiny nozzle that atomizes it into a fine mist. This high compression ratio causes increased cylinder pressures of 400 to 600 psi, which increases the air temperature inside the cylinder so much that it ignites the atomized diesel fuel injected.
Combustion
This mist mixes with air in the combustion chamber and ignites, creating energy to move the piston. The speed of the truck and the power generated by the diesel engine is controlled by the amount of fuel injected into the cylinders. The fuel nozzle on a diesel injector is an important component in the fuel system. Any misadjustment can lead to excessive exhaust smoke, poor fuel economy, heavy carbon building up within the combustion chambers, problems with the aftertreatment system, and even shorter engine life.
Simplicity of the Diesel Fuel Nozzle Pintle Design in Early Injection Diesel Engines (IDI)
The pintle design, prevalent in early Indirect Injection (IDI) diesel engines and numerous gasoline engines, is characterized by an inverted conical tip at the nozzle stem's end, generating a conical spray pattern during fuel atomization.
Positioned strategically in the intake manifold or a dedicated "swirl chamber" within the engine head, this design optimizes the fuel-air mixture before entering the combustion chamber. Despite being associated with older engine technologies, the pintle design stands out for its simplicity and effectiveness in ensuring reliable fuel delivery.
Its historical significance lies in its foundational role in early diesel and gasoline engines, contributing to the evolution of fuel injection engineering and setting the stage for subsequent innovations in the field.
Evolution of the Diesel Fuel Nozzle Multi-Hole Design
The multi-hole fuel nozzle is the most common nozzle used in today’s diesel engines. This nozzle is mounted directly in the combustion chamber, which is a high pressure and elevated temperature environment. If the injector is mounted concentrically in the center of the cylinder, the holes are all in a single plane or ring around the nozzle, equally spaced. If the injector is mounted at an angle, then the holes may be in two different planes, angled so the resulting spray pattern is concentric in the piston. Multi-hole nozzles may have a varying number and size of holes, depending on the combustion chamber, engine size, and horsepower requirements.
Multi-hole nozzles in modern diesel engines exhibit considerable variability to optimize fuel delivery and combustion efficiency. This adaptability is influenced by factors such as combustion chamber geometry, engine size, and horsepower requirements. The configuration of multi-hole nozzles varies, with concentric placement providing a symmetrical spray pattern and angled placement aligning with piston contours.
The number and size of holes in these nozzles are tailored to specific engine needs, allowing for precise control over fuel dispersion. This variability in design reflects a sophisticated approach to fuel injection technology, contributing significantly to the enhanced performance, fuel efficiency, and emissions control observed in contemporary diesel engines.
Fuel Nozzles Optimize Combustion Efficiency
In conclusion, the proper fuel nozzle in a diesel engine ensures precise fuel delivery from the tank to the engine. Whether using the versatile multi-hole design for modern diesel engines or the straightforward pintle design in older engines, fuel nozzles are key to optimizing combustion efficiency. The adaptability of fuel nozzles is crucial in the evolution of engine technology. Understanding the common problems and solutions with fuel nozzles is just as important as appreciating their vital role in diesel engine technology. They are precision tools shaping and optimizing the crucial process of fuel atomization. In turn, they significantly impact the efficiency, performance, and environmental footprint of various engine systems.
Zillion Heavy Duty Parts sells fuel injectors and pumps, aftertreatment, and other engine components. Visit ZillionHD.com for more information on how to become a Zillion distributor. Join us in revolutionizing the trucking industry and creating a future where liberty knows no bounds.